NEW Un-Used BRONZE PLATING LINE-Item#348
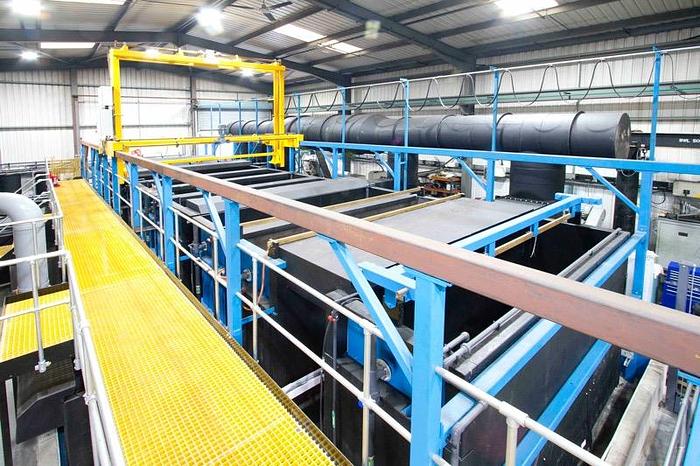
NEW Un-Used BRONZE PLATING LINE-Item#348
Description
BAKER TECHNOLOGY & OUR EUROPEAN PARTNER, RILEY SURFACE WORLD PRESENT NEW Un-Used BRONZE PLATING LINE A newly installed semi-automatic line which is in pristine UNUSED condition. Designed for the application of Bronze Plating on Hydraulic Rams for which it offers good corrosion resistance and surface bearing properties. This line is eminently suitable for conversion to other process applications due to the excellent tank size and complete lack of contamination as it has never been charged with process chemistry. It has unexpectedly come to market before production commissioning could be carried out due to the relocation overseas of the principal customer. The equipment is arranged in a straight line with the Load/Unload station at one end for efficiency of operation. The work is carried through the line by a heavy duty transporter complete with motorized raise lower and traverse which is operator controlled via pendant push buttons. Please note the plant assembly operation ceased as soon as the production requirement was cancelled so some items of tank furniture such as heaters, flight bar locations brackets, DC contacts, pumps et. are supplied loose having not yet been fully fitted. This represents a unique and rare opportunity to acquire an unused line in pristine condition offering considerable savings over the buy new price. TECHNICAL SPECIFICATION Approx. Plant Dimensions: Length: 19.250 M Width: 4.725 M Height: 6.200 M (Excluding Ancillary Equipment) Principle of Operation Components are manually loaded onto the flight bar by an operator at the load station which is provided with a hydraulic raise lower platform. They are then collected by the transporter and transferred through the process under operator control. Each of the three bronze plating tanks are equipped with external pod tanks where chemical additions are made under analytical control. The pod tanks are designed to facilitate solution heating, filtration, pumped circulation from the online tank and mixing of chemical additions. These pod tanks are located in a polypropylene bund tray 5500mm long x 2750mm wide x 250mm deep with inset GRP grid floor panels around the tanks. Bronze process plating time is variable dependent on the thickness of deposit specified on the particular component being plated, between two to ten hours as the thickness range is from 40 to 220 microns. The alkaline cleaner solution is circulated to an offline oil separator tank where the solution temperature is also maintained by electric heaters. Rinse waters weir over from their respective process tanks and flow by gravity to separate acid and cyanide rinse water transfer stations at the end of the line which are fitted with submersible pumps. Incoming mains water for tank top up and rinsing purposes flows by gravity from a dedicated water break tank on support stand adjacent to the line. There are two separate extraction systems one serving the on line process tanks and one serving the off line pod tanks. A raised operator walkway with two sets of access steps, GRP grid way flooring and galvanised steel handrailing runs the length of one side of the line. SPECIFICATION OF EQUIPMENT – 1 off Hydraulic Lift 4000KG SWL with operator controlled raise and lower. Stage will be fitted with: – 1 Off Polypropylene Drip Tray 1 Set Polypropylene flight bar location brackets. 1 Set Galvanised Steel Handrailing Station No. 2 : Process :Hot Water Temperature: 60 o c 1 Off Single compartment tank of internal size 3500mm x 980mm x 2400mm deep, complete with top flange. The body of the tank will be manufactured from mild steel material with 10mm thick base and 8mm thick sides supported with channel belly band strengthening. Tank lined internally with bonded PVC and fitted with 12mm thick PVC base protection sheet. Tank lagged externally and clad with black embossed polypropylene. The tank will be raised off the floor by channel steel support bearers. Tank will be supplied with: Weir overflow to drain manifold. 1 Set Electric heating equipment complete with protection and control. 1 Set Process Temperature Control. 1 Set Polypropylene flight bar location brackets. 1 Set Water supply with manual on/off isolation valve. 1 Set Air agitation. 1 Set Lip Extraction. Station No. 3 : Process : Alkaline Clean :Temperature : 60 o c 1 Off Single compartment tank of internal size 3500mm x 980mm x 2400mm deep, complete with top flange. The body of the tank will be manufactured from mild steel material with 10mm thick base and 8mm thick sides supported with channel belly band strengthening. Tank double welded internally and externally. Tank lagged externally and clad with black embossed polypropylene The tank will be raised off the floor by channel steel support bearers. Tank will be supplied with: Weir overflow to pod tank/ Oil Separator 1 Set Polypropylene flight bar location brackets. 1 Set Water supply with manual on/off isolation valve. 1 Set Brass Cathode Bars with insulation brackets. 1 Set Lip Extraction. Station No. 3A : Offline Pod Tank/Oil Separator : Process : Alkaline Temperature: 60 o c 1 Off Tank of internal size 2000mm x 1000mm x 1200mm deep, complete with top flange. The body of the tank will be manufactured from mild steel material supported with channel belly band strengthening. Tank double welded internally and externally. Tank lagged externally and clad with black embossed polypropylene The tank will be raised off the floor by channel steel support bearers. Tank will be supplied with: Solution inlet by gravity flow from in line process tank. 1 Off In tank vertical pump for solution return to in line process tank. 1 Set under and over weir baffle plates for oil separation. 1 Off Scum weir. 1 Set Electric heating equipment complete with protection and control. 1 Set Process Temperature Control. 1 Set Lip Extraction. Station No. 4 : Process : Alkaline Rinse : Temperature: AMB 1 Off Single compartment tank of internal size 3500mm x 980mm x 2400mm deep, complete with top flange. The body of the tank will be manufactured from mild steel material with 10mm thick base and 8mm thick sides supported with channel belly band strengthening. Tank lined internally with bonded PVC and fitted with 12mm thick PVC base protection sheet. The tank will be raised off the floor by channel steel support bearers. Tank will be supplied with: Weir overflow to drain manifold. 1 Set Polypropylene flight bar location brackets. 1 Set Water supply with manual on/off isolation valve 1 Set Air agitation. Station No. 5 : Process Acid Etch : Temperature: 55 o c 1 Off Single compartment tank of internal size 3500mm x 980mm x 2400mm deep, complete with top flange. The body of the tank will be manufactured from mild steel material with 10mm thick base and 8mm thick sides supported with channel belly band strengthening. Tank lined internally with bonded PVC and fitted with 12mm thick PVC base protection sheet. Tank lagged externally and clad with black embossed polypropylene. The tank will be raised off the floor by channel steel support bearers. Tank will be supplied with: 1 Set Electric heating equipment complete with protection and control. 1 Set Process Temperature Control. 1 Set Polypropylene flight bar location brackets. 1 Set Water supply with manual on/off isolation valve 1 Set Lip Extraction. Station No. 6 : Process : Acid Rinse : Temperature: AMB 1 Off Single compartment tank of internal size 3500mm x 980mm x 2400mm deep, complete with top flange. The body of the tank will be manufactured from mild steel material with 10mm thick base and 8mm thick sides supported with channel belly band strengthening. Tank lined internally with bonded PVC and fitted with 12mm thick PVC base protection sheet. The tank will be raised off the floor by channel steel support bearers. Tank will be supplied with: Weir overflow to drain manifold. 1 Set Polypropylene flight bar location brackets. 1 Set Water supply with manual on/off isolation valve 1 Set Air agitation. Station No. 7 : Process : Cyanide Dip : Temperature: AMB 1 Off Single compartment tank of internal size 3500mm x 980mm x 2400mm deep, complete with top flange. The body of the tank will be manufactured from mild steel material with 10mm thick base and 8mm thick sides supported with channel belly band strengthening. Tank lined internally with bonded PVC and fitted with 12mm thick PVC base protection sheet. The tank will be raised off the floor by channel steel support bearers. Tank will be supplied with: 1 Set Polypropylene flight bar location brackets. 1 Set Water supply with manual on/off isolation valve Station No. 8 : Process : Cyanide Rinse : Temperature: AMB 1 Off Single compartment tank of internal size 3500mm x 980mm x 2400mm deep, complete with top flange. The body of the tank will be manufactured from mild steel material with 10mm thick base and 8mm thick sides supported with channel belly band strengthening. Tank lined internally with bonded PVC and fitted with 12mm thick PVC base protection sheet. The tank will be raised off the floor by channel steel support bearers. Tank will be supplied with: Weir overflow to drain manifold. 1 Set Polypropylene flight bar location brackets. 1 Set Water supply with manual on/off isolation valve 1 Set Air agitation. Station No. 9 : Process : Bronze Electroplate : Temperature: 65 o c 1 Off Single compartment tank of internal size 3500mm x 980mm x 2400mm deep, complete with top flange. The body of the tank will be manufactured from mild steel material with 10mm thick base and 8mm thick sides supported with channel belly band strengthening. Tank lined internally with bonded PVC and fitted with 12mm thick PVC base protection sheet. Tank lagged externally and clad with black embossed polypropylene. The tank will be raised off the floor by channel steel support bearers. Tank will be supplied with: Weir overflow to pod tank. 3 Pairs Spring loaded cathodic flight bar location brackets. 1 Set Brass anode rails with cross connectors and insulation brackets. 1 Set Water supply with manual on/off isolation valve 1 Set Eductor agitation. 1 Set Lip Extraction. Station No. 9A : Offline Pod/Conditioning Tank : Process : Bronze Electroplate : Temperature: 65 o c 1 Off Tank of internal size 2000mm x 1200mm x 1200mm deep, complete with top flange. The body of the tank will be manufactured from mild steel material supported with channel belly band strengthening. Tank double welded internally and externally. Tank lagged externally and clad with black embossed polypropylene The tank will be raised off the floor by channel steel support bearers. Tank will be supplied with: Solution inlet by gravity flow from in line process tank. 2 Off In tank vertical pumps for solution return to in line process tank. 1 Set Bag Filtration with distribution pipework. 1 Off Electric motor driven mixer with stainless steel shaft and impellor. 1 Set Electric heating equipment complete with protection and control. 1 Set Process Temperature Control. 1 Set Lip Extraction. Station No. 10 : Process : Bronze Electroplate :Temperature : 65 o c 1 Off Single compartment tank of internal size 3500mm x 980mm x 2400mm deep, complete with top flange. The body of the tank will be manufactured from mild steel material with 10mm thick base and 8mm thick sides supported with channel belly band strengthening. Tank lined internally with bonded PVC and fitted with 12mm thick PVC base protection sheet. Tank lagged externally and clad with black embossed polypropylene. The tank will be raised off the floor by channel steel support bearers. Tank will be supplied with: Weir overflow to pod tank. 1 Set Water supply with manual on/off isolation valve 1 Set Lip Extraction. Station No. 10A :Offline Pod/Conditioning Tank : Process : Bronze Electroplate : Temperature: 65 o c 1 Off Tank of internal size 2000mm x 1200mm x 1200mm deep, complete with top flange. The body of the tank will be manufactured from mild steel material supported with channel belly band strengthening. Tank double welded internally and externally. Tank lagged externally and clad with black embossed polypropylene The tank will be raised off the floor by channel steel support bearers. Tank will be supplied with: Solution inlet by gravity flow from in line process tank. 1 Set Bag Filtration with distribution pipework. 1 Off Electric motor driven mixer with stainless steel shaft and impellor. 1 Set Electric heating equipment complete with protection and control. 1 Set Process Temperature Control. 1 Set Lip Extraction. Station No. 11 : Process : Bronze Electroplate : Temperature : 65 o c 1 Off Single compartment tank of internal size 3500mm x 980mm x 2400mm deep, complete with top flange. The body of the tank will be manufactured from mild steel material with 10mm thick base and 8mm thick sides supported with channel belly band strengthening. Tank lined internally with bonded PVC and fitted with 12mm thick PVC base protection sheet. Tank lagged externally and clad with black embossed polypropylene. The tank will be raised off the floor by channel steel support bearers. Tank will be supplied with weir overflow to pod tank. 1 Set Water supply with manual on/off isolation valve 1 Set Lip Extraction. Station No. 11A : Offline Pod/Conditioning Tank : Process : Bronze Electroplate : Temperature: 65 o c 1 Off Tank of internal size 2000mm x 1200mm x 1200mm deep, complete with top flange. The body of the tank will be manufactured from mild steel material supported with channel belly band strengthening. Tank double welded internally and externally. Tank lagged externally and clad with black embossed polypropylene The tank will be raised off the floor by channel steel support bearers. Tank will be supplied with: Solution inlet by gravity flow from in line process tank. 1 Set Bag Filtration with distribution pipework. 1 Off Electric motor driven mixer with stainless steel shaft and impellor. 1 Set Electric heating equipment complete with protection and control. 1 Set Process Temperature Control. 1 Set Lip Extraction. DRIP SHIELDS Tanks not fitted with exhaust ducts have PVC drip shields in between to stop solution spillage. SUPPORT TANKS Three off support tanks in black polypropylene are located adjacent to the line. One being incoming mains water supply break tank the other two being acid and cyanide rinse water transfer tanks fitted with submersible pumps. TRANSFER THROUGH PROCESS STATIONS TRANSPORTER EQUIPMENT 1 Off Fully motorised 1500kg SWL heavy duty twin track transporter system, to operate in semi-automatic mode. The transporter is manufactured in mild steel RHS, and other steel sections all painted in hazard warning yellow. The mast is 3600mm vertically and the horizontal carriage 2000mm long. The track centres are 4625mm on which run the two driven and two idler urethane tired wheels. The hoist is by means of twin lifting chains running in sprockets inside the masts at each side with a cross shaft at hight level to the geared motor. Power feed to the transporter via festoon cable catenary system. All transporter movements are initiated by the operator using a manual pendant control unit and will be controlled and monitored to ensure that all safety interlocks remain active. For example, pressing the forward button on the pendant will cause the transporter to move forward until the button is released. At this point the transporter will continue to move forward until it reaches the next station flag, where it will stop when the on station proximity switches are in contact with the flag. However, striking over travel limit switches at any time will stop the travel or hoist motor. TRACK SUPPORT STRUCTURE The heavy duty twin track gantry system is manufactured from 100mm x 150mm mild steel RHS beams supported by 100mm x 100mm mild steel RHS stanchions from the floor. Cross bracing is provided as required. The self-supporting structure is in bolted sections lined and levelled on to the factory floor without the need for special foundations. The down shop runway length is 19255mm, the track centres are 4625mm and the track height from factory floor level is 3550mm. WALKWAY The full length of one side of the main process line is served by a raised operator walkway 17400mm long x 1010mm wide x 1800mm above factory floor level. The walkway has two sets of access stairways, GRP grid flooring and galvanised steel handrailing. FUME EXHAUST SYSTEMS SCOPE OF SUPPLY Two fume exhaust systems are installed one for the in-line processes and one for the offline pod/conditioning tanks. Each extraction system includes the following major items of equipment: – Fume exhaust hoods Interconnecting trunking Exhaust Fans Outlet stacks SPECIFICATION OF EQUIPMENT System One Main Line Item 1 – Lip Extract Hoods – 5 Off 4 off Single sided and one off double sided lip extraction ducts fitted above tank rim with full length slots fitted with plenum chamber and drain point. Item 2 – Ductwork Flanged connection risers to main manifold. Manifold with the header duct run at high level The header manifold has a central offtake branch routed horizontally outside through the external factory wall. All ductwork supplied complete with supports, hangers, brackets, fasteners and fixings. Item 3 – Extraction Fan Centrifugal fume exhaust fan, vee driven from three phase 22kW motor complete with base frame and drain socket. Fan casing fabricated in Polypropylene / GRP Impeller fabricated in Polypropylene. Base frame etc. fabricated in mild steel and painted finish. Item 4 – Discharge Stack Fume discharge stack terminating with an Efflux cone. Fabricated in welded sections of black embossed polypropylene supplied with all brackets, stays, guys, gaskets, fixings. System Two, Offline Pod and Conditioning Tanks Item 1 – Lip Extract Hoods – 4 Off 4 off Single sided lip extraction ducts fitted above tank rim with full length slots fitted with plenum chamber and drain point. Item 2 – Ductwork – Flanged connection risers to main manifold. Manifold with the header duct run at high level. The header manifold is routed horizontally outside through the external factory wall. Material of construction: – Internal Black Embossed & Grey Polypropylene. External PVC. All ductwork supplied complete with supports, hangers, brackets, fasteners and fixings. Item 3 – Extraction Fan Centrifugal fume exhaust fan, direct driven from three phase 5.5kW motor complete with base frame and drain socket. Fan casing fabricated in PVC Impeller fabricated in PVC. Base frame etc. fabricated in mild steel and painted finish. Item 4 – Discharge Stack Fume discharge stack terminating with an Efflux cone. Fabricated in welded sections of PVC supplied with all brackets, stays, guys, gaskets, fixings. CONTROL CONSOLE The central control console is located adjacent to the load/unload area and contains, door interlocking isolator, contactors, circuit breakers and rail mounted terminal blocks There are six off door mounted electronic temperature controllers for the heated process tanks complete with heater on/off switches and low level indication. The controls for the pumps and stirrers are also mounted on the cabinet doors. ELECTRICAL WIRING All electrical wiring between the central control console and field electrical items is installed in corrosion resistant PVC or galvanised-steel cable tray suitably supported. MECHANICAL SERVICES One set mechanical services serving the previously described plant complete with all necessary supports and brackets.
Specifications
Condition | New |
Stock Number | 348 |
Plant design | Straight Line Semi-Automatic Plant. |
Process | Bronze Electroplate |
Base metal of components | High Strength Steel |
Components | Hydraulic Rams |
Operation | Semi-Automatic |
Estimated plant output | Variable |
Tank section | 3500mm wide x 2400mm deep |
Transporter | One 1500kg SWL Transporter |
Hoist motor | Pendant Push Button Control |
Traverse motor | Pendant Push Button Control |
Flight bars | 1 off included |
Heating | Electric |
Electrical supply | 415v 50hz 3ph with neutral |
Station no.1 | Load/Unload Station |
Material of construction | – Black Embossed Polypropylene |